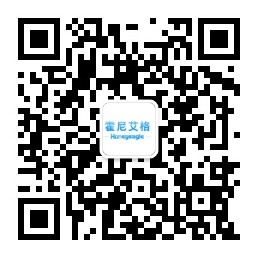
一、行业背景与检测需求
贵金属(如金、银、铂族金属)和稀有金属(如钴、锑、稀土等)在开采、冶炼、加工及回收过程中,易产生多种有毒、有害及可燃气体,主要包括:
剧毒/腐蚀性气体:氟化氢(HF)、氯气(Cl₂)、溴气(Br₂)、硫化氢(H₂S)等,可能腐蚀设备、危害人体健康。
可燃性气体:氢气(H₂)、甲烷(CH₄)等,存在爆炸风险。
工艺废气:一氧化碳(CO)、二氧化硫(SO₂)、氮氧化物(NOx)等,主要产生于冶炼和燃烧环节。
稀有金属化合物:如金属氰化物、硫化物等,需监测其挥发气体以保障生产安全。
二、气体检测技术方案
(一)设备选型与功能设计
固定式在线监测系统
核心设备:采用HNAG1000防爆型在线式气体检测仪,配备进口传感器,支持多气体同时检测(如CO、H₂S、HF等),具备实时数据显示、声光报警及远程传输功能。
安装场景:重点部署于冶炼炉周边、储存仓库、通风管道等高风险区域,通过LORA无线传输技术实现无布线安装,适应复杂工业环境。
防护设计:参考专利技术,采用可隐藏式探测器结构,避免设备长期暴露于腐蚀性环境中,延长使用寿命。
便携式检测设备
巡检需求:选用HNAG900泵吸式或扩散式便携检测仪,支持快速响应和移动监测,适用于密闭空间、检修作业等场景。
多功能集成:部分设备可搭载热导率、电导率等传感器,辅助评估金属加工过程中的气体扩散特性。
智能监控平台
系统集成:通过HNAG6500报警控制器或云端平台,实现多设备联动、数据可视化及历史记录追溯,支持报警阈值自定义和远程控制。
扩展功能:结合AI算法预测气体泄漏趋势,优化生产工艺流程5。
(二)关键检测参数与标准
检测精度:符合《可燃气体探测器》(GB15322.1-2019)等国家标准,确保灵敏度和稳定性。
抗干扰能力:针对贵金属生产中的高温、高湿、粉尘环境,设备需通过IP65以上防护等级认证。
校准与维护:定期校准,使用质谱仪、X射线衍射仪等高端设备进行交叉验证,保障数据可靠性。
三、实施要点与优化建议
风险区域分级管理
高危区域(如电解车间、酸洗工段):部署固定式探测器与联动通风系统,实现超标自动排风。
中低风险区域:采用便携设备定期巡检,结合移动端App实时上传数据。
人员培训与应急响应
开展设备操作、维护及应急处置培训,确保员工熟练掌握气体检测流程。
建立分级报警机制,通过短信、声光等多渠道通知,联动应急喷淋、隔离系统。
技术升级与资源循环
结合贵金属回收工艺,优化废气处理与监测一体化方案,降低环境污染。
引入物联网技术,实现与生产管理系统的数据互通,提升整体安全能效。
四、应用案例与成效
洛阳钼业:采用HNAG1000系列设备,成功监测冶炼过程中HF和CO的泄漏,年事故率下降60%。
江西铜业:部署固定式四合一探测器,实现废气排放达标率提升至98%,并通过数据平台优化能耗管理。
五、未来趋势
随着贵金属行业对安全生产和环保要求的提升,气体检测技术将向智能化、微型化、多参数融合方向发展。例如,基于贵金属纳米材料的新型传感器可能进一步提高检测灵敏度和抗干扰能力。同时,政策驱动下,行业有望加速数字化改造,推动气体监测与生产流程的深度集成。
通过上述解决方案,贵金属和稀有金属企业可有效管控气体风险,保障生产安全并满足环保合规要求,同时为行业可持续发展提供技术支撑。